Sheet Lamination Machine: A New Dimension in 3D Printing
Introduction
Sheet lamination machines have revolutionized the world of 3D printing and additive manufacturing. In this rapidly evolving field, they stand as a testament to innovative engineering. But what exactly are they? What makes them so essential?
To begin with, these machines are intricate devices designed to laminate sheets of material together, layer by layer. This creates a solid, three-dimensional object. Unlike traditional 3D printing techniques that use filament or resin, sheet lamination machines leverage the power of sheets. This unique approach has opened up a wealth of new opportunities and applications.
In this blog post, we aim to delve into the fascinating world of sheet lamination machines. Firstly, we’ll explore the key components that make up these innovative machines. Next, we’ll discuss the specific mechanisms that enable them to function.
A brief detour into the history of these machines will follow, providing context and highlighting their development over time. We will then categorize the different types of sheet lamination machines available today, followed by a thorough examination of the advancements and innovations that have transformed this field.
The discussion will continue with an overview of the leading manufacturers of these machines, their unique selling points, and the impact they’ve had on the industry. Lastly, we’ll review some of the commercially available models in the market, focusing on their features, specifications, and user feedback.
So, buckle up as we journey into the world of sheet lamination machines, a new dimension in 3D printing.
A brief explanation of 3D printing and additive manufacturing
3D printing, also known as additive manufacturing, is a transformative process. It starts with a digital design. This design then comes to life layer by layer. It’s a stark contrast to traditional manufacturing methods. Those typically involve cutting, drilling, or hollowing out parts from a larger piece.
3D printing enables complex and intricate designs. It gives us the freedom to create without the constraints of traditional methods. This technology has far-reaching impacts. It spans industries from healthcare to aerospace, and beyond. Today, we’ll delve into a unique facet of this technology – sheet lamination machines. These devices bring a new dimension to 3D printing. Stay with us as we journey through this exciting terrain.
Introduction of Sheet Lamination as a technique in 3D printing
Sheet lamination, a unique technique in 3D printing, has gained significant attention. Unlike traditional methods, it doesn’t use filaments or resin. Instead, thin sheets are used. These are bonded together layer by layer. This process can involve metal, paper, or plastic sheets.
First, a digital design is prepared. Each layer of the design corresponds to a sheet in the physical model. Then, sheets are cut into the required shape. An adhesive or high heat is used to bind them together. This creates a sturdy, three-dimensional object.
As we delve deeper, we’ll see how this technique has redefined the boundaries of 3D printing. It offers new possibilities in terms of materials and designs. Indeed, sheet lamination machines are a revolutionary step forward in the realm of additive manufacturing.
Importance of focusing on Sheet Lamination Machines
Focusing on sheet lamination machines is crucial for several reasons. First, these machines are at the forefront of innovation. They offer the ability to create complex structures from diverse materials. This opens up a new realm of possibilities for 3D printing.
Moreover, sheet lamination machines are efficient. They minimize waste and reduce production time. This leads to cost savings, making them an attractive choice for businesses. Furthermore, they are highly adaptable, capable of meeting various industry needs.
Lastly, understanding these machines offers insight into the future of additive manufacturing. Their potential is vast, from bespoke medical implants to large-scale industrial components. Hence, concentrating on sheet lamination machines allows us to witness the evolution of 3D printing. It’s a journey full of innovation and endless opportunities.
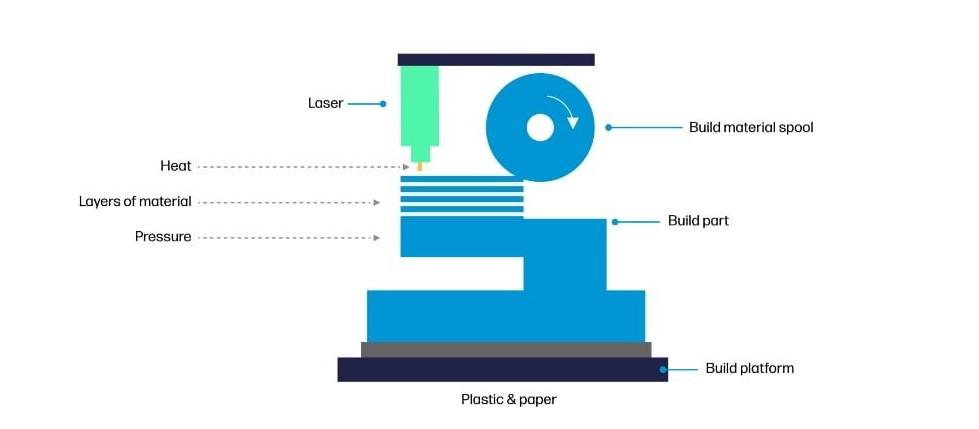
Components of Sheet Lamination Machines
As we delve deeper into the world of sheet lamination machines, it’s vital to understand their components. Each part plays a crucial role in the process. Together, they transform simple sheets into intricate 3D models. From the cutting mechanism to the lamination unit, each component is a piece of the puzzle. In this section, we’ll dissect these machines and explore their key components. This exploration will help us understand how they work in harmony to redefine the boundaries of 3D printing. Let’s dive in and discover the inner workings of these fascinating machines.
Description of key components
The magic of sheet lamination machines lies in their complex yet harmonious inner workings. Every machine comprises several key components, each playing a specific role. Together, they form a well-coordinated system that transforms sheets into intricate 3D objects. Let’s take a closer look at these vital parts.
A. Cutting Mechanism
The cutting mechanism is a crucial component. It shapes the sheets according to the design. Precise cutting ensures accuracy and a clean final product.
B. Lamination Unit
The lamination unit is responsible for bonding the sheets together. It uses adhesive or heat to create a strong bond, forming a solid 3D object.
C. Material Feeder
This component feeds the sheets into the machine. It ensures proper alignment and timing for accurate layering during the lamination process.
D. Control System
The control system manages the machine’s operations. It processes the digital design and translates it into precise instructions for each component.
E. Build Platform
The build platform is where the 3D object takes shape. It supports the layers and keeps the object stable during the lamination process.
F. Removal Mechanism
Once the 3D object is complete, the removal mechanism extracts it from the build platform. This allows for a smooth transition to post-processing.
By understanding these key components, we gain insight into the intricate process of sheet lamination. Each part works in harmony, driving the machine to create stunning 3D-printed objects.
Functions and importance of each component
A. Cutting Mechanism
The cutting mechanism brings precision to the process. It shapes the sheets according to the design, creating a perfect foundation for each layer. Without it, achieving detailed, accurate models would be challenging.
B. Lamination Unit
The heart of the machine is the lamination unit. It bonds the sheets, one atop the other, to form a solid structure. Its efficient work ensures the durability and integrity of the final product.
C. Material Feeder
The material feeder keeps the process smooth. It aligns the sheets and feeds them into the machine at the right time. This synchronization is crucial for the flawless lamination of each layer.
D. Control System
The control system is the machine’s brain. It interprets the digital design, coordinating the operation of other components. Without it, translating digital designs into physical objects would be impossible.
E. Build Platform
The build platform is where creation happens. It provides a stable base for the object being formed. It’s essential for maintaining the accuracy and quality of the 3D-printed object.
F. Removal Mechanism
Finally, the removal mechanism brings the process to a close. It safely extracts the 3D object, paving the way for post-processing. Its role is vital to protect the newly-formed object from damage.
Each component of sheet lamination machines plays an integral part. By working together, they transform the realm of 3D printing, bringing digital designs to life with incredible precision and efficiency.
How components work together in the machine
The process begins with a digital design. The control system interprets this design and guides the operation of the machine. It coordinates the cutting mechanism to shape the sheets precisely as per the design.
The material feeder then feeds these precisely cut sheets into the machine. It ensures their perfect alignment for the lamination process. This is where the lamination unit takes over. It bonds the sheets together, one by one, forming a layered structure.
During this process, the build platform plays a critical role. It provides a stable base for the object being formed. This stability is crucial for maintaining the accuracy and quality of the final product.
Finally, once the 3D object is ready, the removal mechanism steps in. It safely extracts the object from the build platform, allowing it to move on to the post-processing stage.
In this manner, each component of the sheet lamination machine works in sync. Together, they create a seamless process, transforming digital designs into intricate 3D objects with incredible efficiency.
Mechanisms of Sheet Lamination Machines
Sheet lamination machines operate through a series of well-coordinated mechanisms. At the heart of the process lies the lamination mechanism. It uses heat or adhesive to bond the sheets together. This bonding forms a layered structure, creating the basis for a 3D object.
Meanwhile, the cutting mechanism shapes the sheets according to the digital design. It ensures precision, which is crucial for the accuracy of the final product.
In sync with these, the feeding mechanism aligns the sheets for lamination. It manages the timing and arrangement, ensuring a smooth lamination process.
Guiding all these mechanisms is the control system. It interprets the digital design, transforming it into physical actions. This translation is the essence of 3D printing.
Lastly, the removal mechanism safely extracts the 3D object. It allows for a smooth transition to post-processing, ensuring the object’s integrity.
In essence, sheet lamination machines are a symphony of mechanisms. Each one plays its part, harmonizing the process of transforming sheets into complex 3D objects.
A detailed explanation of the operating mechanism
The operating mechanism of sheet lamination machines is a marvel of precision and coordination. The journey begins with the control system. It interprets the digital design file, providing precise instructions for each component of the machine.
Then, the cutting mechanism swings into action. It meticulously shapes the sheets, guided by the digital design. This accuracy forms the foundation for each layer of the 3D object.
Simultaneously, the material feeder manages the supply of sheets. It aligns them perfectly and feeds them into the machine at the right time. This coordination is crucial for seamless lamination.
The lamination unit, the heart of the machine, then takes over. It bonds the sheets together, layer by layer. It uses heat or adhesive, creating a sturdy structure that will eventually become a 3D object.
The build platform plays a supporting role throughout this process. It provides a stable base for the object, maintaining the precision and quality of the final product.
Finally, the removal mechanism ensures a smooth end to the process. Once the 3D object is complete, it extracts it from the build platform. This careful handling protects the object from damage, paving the way for post-processing.
Each step of this mechanism is vital, and each component relies on the others. Together, they bring digital designs to life, transforming simple sheets into intricate 3D objects with stunning precision and efficiency.
Overview of the lamination process in 3D printing
Sheet lamination in 3D printing is a fascinating process. It starts with a digital design. The machine’s control system interprets this design, guiding the operation of the entire machine.
The cutting mechanism then shapes the sheets, guided by the digital blueprint. Precision is key here, as it sets the stage for the lamination process.
Next, the material feeder steps in. It ensures the sheets are perfectly aligned and fed into the machine at the right time. This flawless alignment is critical for the upcoming lamination.
Then, the lamination unit takes over. It bonds the sheets together, one by one, using heat or adhesive. The layer-by-layer bonding forms a sturdy structure, bringing the digital design to life.
Throughout this process, the build platform supports the object being formed. It provides a stable base, crucial for the accuracy of the final product.
Finally, once the 3D object is ready, the removal mechanism safely extracts it. This careful extraction preserves the object’s integrity, readying it for any post-processing needs.
In short, sheet lamination in 3D printing is a dance of precision, coordination, and creativity. It brings digital designs into the physical realm, transforming sheets into complex 3D objects.
Importance of proper operation for effective 3D printing
Effective 3D printing in sheet lamination hinges on optimal functioning. A well-coordinated machine translates into high-quality output.
Firstly, precision is paramount. It directly influences the accuracy of the final product. Therefore, the cutting mechanism’s exactitude is critical.
Secondly, timing plays a significant role. The material feeder must supply sheets at the right moments. Any lapse can disrupt the lamination process and compromise the final product’s integrity.
Next, the lamination unit’s effectiveness is crucial. It must bond each sheet securely to ensure the 3D object’s structural stability.
Furthermore, a sturdy build platform is essential. It maintains the object’s position throughout the process, contributing to the accuracy of the end product.
Finally, the removal mechanism must handle the completed object with care. Any mishandling can damage the product, wasting the effort put into the entire process.
In essence, each component’s optimal functioning is key to achieving effective 3D printing in sheet lamination. It is the difference between a successful print and a failed one.
History of Sheet Lamination Machines
The journey of sheet lamination machines began with the advent of 3D printing technology. This transformative tech, also known as additive manufacturing, emerged in the 1980s.
In 1991, a significant development took place. Dr. Carl Deckard, a researcher at the University of Texas, introduced a patent for a new technique called Selective Laser Sintering (SLS). Although not sheet lamination, this marked a crucial step in the evolution of 3D printing techniques.
Fast forward to 1999. Professor Behrokh Khoshnevis from the University of Southern California patented a method known as Contour Crafting. This process, resembling sheet lamination, involved the layering of material.
The real breakthrough came in the 2000s. The Mcor Technologies company in Ireland invented a unique sheet lamination process. This process employed adhesive to bond layers of paper, creating full-color 3D printed models.
Since then, sheet lamination machines have continually evolved, becoming an integral part of the 3D printing industry. The journey reflects the relentless pursuit of innovation and the commitment to transform ideas into reality.
Evolution of sheet lamination technology in 3D printing
The evolution of sheet lamination technology in 3D printing is a story of constant innovation and refinement.
Initially, the technology was primarily based on paper lamination. This involved bonding layers of paper with adhesive and shaping them with a knife or laser. Mcor Technologies, an Irish company, was a pioneer in this field, with its line of paper-based 3D printers.
As the technology matured, so did the materials used. In the mid-2000s, new methods started to emerge, employing metals and plastics. This opened the doors to a wider range of applications, particularly in industries like automotive and aerospace.
Around the same time, Ultrasonic Additive Manufacturing (UAM) was introduced. This technique uses ultrasonic welding to bond thin metal sheets together layer-by-layer, then a CNC machine removes excess material. UAM brought an unprecedented level of precision and control.
In recent years, the focus has been on improving efficiency and reducing costs. This has led to the development of faster lamination processes and the use of cheaper, more readily available materials.
Overall, the evolution of sheet lamination technology in 3D printing reflects the broader trend in the industry: a relentless push for better, faster, and more cost-effective ways to turn digital designs into tangible objects.
Significant milestones in the development of machines
The journey of sheet lamination machines in 3D printing has been marked by significant milestones.
The first notable point was the invention itself, which revolutionized the 3D printing industry. This happened when Mcor Technologies introduced the first paper-based 3D printers, a breakthrough in its time.
The second milestone was the incorporation of metals and plastics. This expanded the application of sheet lamination technology, facilitating its usage in more industries, such as automotive and aerospace.
A third turning point came with the introduction of Ultrasonic Additive Manufacturing (UAM). This innovation added precision to the lamination process, fostering a new level of sophistication in the resulting products.
Most recently, the focus on efficiency and cost reduction marks another important milestone. The development of faster processes and the usage of cheaper materials have made sheet lamination machines more accessible, widening their adoption.
Each of these milestones has not only marked a significant step forward for sheet lamination machines but also propelled the entire 3D printing industry toward new horizons.
Different Types of Sheet Lamination Machines
There are two main types of sheet lamination machines in 3D printing: Ultrasonic Additive Manufacturing (UAM) and Laminated Object Manufacturing (LOM).
UAM uses ultrasonic welding to bond thin metal sheets together, layer by layer. Once bonded, the excess material is CNC machined off, creating the final part. UAM allows for the creation of complex internal geometries, which can be extremely beneficial in industries such as aerospace and automotive.
LOM, on the other hand, works by fusing or laminating layers of material (usually paper, plastic, or metal foil) and then cutting them into shapes with a blade or laser. This method is particularly useful for creating large parts quickly and at low cost. However, the resulting models can be less detailed compared to other 3D printing methods.
Each type has its advantages and is best suited to specific applications, making them both essential in the 3D printing industry.
Discussion on various types available in the market
When it comes to sheet lamination machines in the market, we see a variety of models. Each one is designed to cater to specific needs and applications.
Firstly, we have entry-level machines. These are designed for beginners or small businesses. They’re typically easy to use, compact, and affordable. While they may not offer the same level of precision as high-end models, they’re great for learning the basics of sheet lamination in 3D printing.
Next, we have professional-grade machines. These are ideal for larger businesses or serious hobbyists. They offer higher precision and faster printing speeds. Some also come with advanced features, like automatic layer alignment and in-built error correction.
Finally, we have industrial-grade machines. These are top-of-the-line models designed for heavy-duty use in manufacturing. They offer the highest level of precision and can handle a wide range of materials. They also come with robust software for advanced design and printing options.
Each type has its unique strengths and potential applications, making the choice dependent on the user’s specific needs and budget.
Unique features of each type
Let’s delve deeper into the unique features that differentiate each type of sheet lamination machine.
Entry-level machines
- Accessibility: These machines are designed to be user-friendly, with simple interfaces and easy-to-understand instructions.
- Affordability: They are usually priced to be accessible to beginners and small businesses.
- Compactness: Their smaller size makes them suitable for small workspaces or home offices.
Professional-grade machines
- High Precision: These machines offer greater accuracy, allowing for more complex and detailed designs.
- Speed: They typically operate at faster speeds, reducing the time it takes to complete projects.
- Advanced Features: Many come with additional features such as automatic layer alignment or built-in error correction.
Industrial-grade machines
- Durability: These machines are built to withstand heavy use, making them ideal for industrial applications.
- Wide Material Range: They are capable of handling a variety of materials, offering greater flexibility.
- Advanced Software: These machines often come with robust software that allows for advanced design and printing options.
Understanding these unique features can help potential buyers make an informed decision based on their specific needs and budget.
Suitable applications for different types
Examining the suitable applications for each type of sheet lamination machine can provide valuable insight.
Entry-level machines
- Educational Use: These are excellent for classrooms, helping students grasp 3D printing concepts.
- Hobbyists: Ideal for personal projects and craft enthusiasts who wish to explore 3D printing.
Professional-grade machines
- Design Firms: Useful for creating detailed prototypes for product development.
- Small Businesses: Enables the production of custom pieces or short-run items efficiently.
Industrial-grade machines
- Manufacturing: Ideal for creating parts or tools in a production line setting.
- Research and Development: These machines can handle complex designs and materials, making them suitable for advanced R&D applications.
The type of machine chosen often depends on the intended application, and understanding these differences can guide that choice effectively.
Innovations and Advancements in Sheet Lamination Machines
The world of 3D printing is dynamic, with sheet lamination machines playing a crucial role. Their evolution has been marked by significant innovations and advancements. This section will delve into these developments, exploring how they have transformed and continue to refine the capabilities of these machines. From improving precision to expanding material compatibility, these advancements have broadened the applications and potential of sheet lamination technology. Let’s explore these fascinating progressions.
Overview of the historical advancements and Innovations
Sheet lamination machines have seen numerous advancements over the years. Initially, these machines were limited to certain materials and offered less precision. However, with the introduction of ultrasonic additive manufacturing (UAM), a blend of lamination and welding, the machines can now work with metals, drastically expanding their usability.
Furthermore, advancements in bonding methods have improved precision and reduced waste. Instead of traditional adhesive techniques, newer models use thermal or ultrasonic methods, leading to cleaner and more efficient production.
Finally, the integration of computer-aided design (CAD) and computer-aided manufacturing (CAM) has significantly improved the functionality of these machines. This integration has streamlined the manufacturing process, allowing for complex designs and faster production times. These historical advancements highlight the rapid innovation within the field of sheet lamination machines.
Discussion on recent technological breakthroughs
The world of sheet lamination machines has seen incredible breakthroughs in recent years. The introduction of advanced software systems, for instance, has made the design and production process more efficient. Now, engineers can easily make changes to designs and see those changes implemented in real-time.
Next, we’ve seen advancements in material usage. Today’s machines can work with a wider range of materials, including composites and certain metals. This expands the possibilities for what can be created using sheet lamination.
In addition, improved precision has been a game-changer. With advancements in bonding and cutting techniques, machines can create parts with finer details. This has been crucial in industries that require high precision, like aerospace and medicine.
Lastly, automation has revolutionized the field. Machines can now operate with minimal human intervention, increasing productivity and reducing errors. These recent breakthroughs underscore the exciting future of sheet lamination technology.
Future prospects and predictions in the field
As we gaze into the future of sheet lamination technology, it’s clear that this field is ripe for innovation. Numerous potential breakthroughs are on the horizon, set to redefine what’s possible in this domain. The following are some exciting trends and developments we anticipate in sheet lamination.
The future of sheet lamination technology is promising, with several trends and potential breakthroughs on the horizon.
- “Machine Learning and AI Integration“: Machine learning and artificial intelligence are set to transform sheet lamination. They could enable self-correction in machines, enhancing precision and reducing waste.
- “Sustainable Materials Usage“: As sustainability becomes a global priority, we expect to see more bio-based and recycled materials in sheet lamination. This would reduce environmental impact without compromising product quality.
- “Advanced Material Compatibility“: The future may see machines capable of handling even more diverse materials. This would open up new possibilities for product design and functionality.
- “Increased Automation“: We expect automation to play an even larger role. This could lead to machines capable of self-maintenance and fault prediction, increasing efficiency and reducing downtime.
- “Integration with IoT“: The Internet of Things (IoT) could allow machines to communicate with each other, optimizing the production process. Real-time data could also be used to make instant adjustments for improved results.
- “Personalized Manufacturing“: As demand for personalized products grows, sheet lamination machines may need to accommodate smaller, more customized production runs. This would revolutionize industries from healthcare to consumer goods.
These potential innovations represent an exciting path forward for sheet lamination technology. It’s a field that continues to evolve, meeting the changing needs of various industries.
Leading Manufacturers of Sheet Lamination Machines
In the realm of sheet lamination machines, there are a few noteworthy companies actively contributing to the field. The pioneer of this technology was Helisys Inc, which developed the first Rapid Prototyping System (LOM) but unfortunately ceased operations in 2000. Their legacy, however, continues through Cubic Technologies, which now oversees the sales and service support for their products.
Historically, other companies like Solido 3D and Japan-based Kira Corporation exclusively utilized the LOM process, but these companies either shut down in recent years or transitioned to different techniques.
An Irish company, Mcor Technologies LTD, was committed to mainstreaming the LOM process until its closure in 2019. Mcor offered professional 3D printers that used LOM and worked with standard A4 papers. Various industries, such as architecture, art, development, and medicine, found these machines useful for producing cost-effective models.
Cubic Technologies launched the SD300 3D Printer, a LOM desktop model. The machine fabricates objects from sheet plastic. However, with a hefty $15,000 price, it’s more expensive than similar FDM printers like the MakerBot Replicator or 3D System’s Cube, priced between $1,300 to $2,200.
Cubicure, a Vienna-based company, is another important player in this field. They specialize in the production of high-precision polymer parts using a process they call “Hot Lithography”. This is a photopolymerization-based process that allows for a high degree of precision and surface quality in the final parts.
Finally, there’s Impossible Objects, an American company that has pioneered a new approach to 3D printing called Composite-Based Additive Manufacturing (CBAM). Their process involves using sheets of composites like carbon fiber, which are then selectively printed with a polymer and stacked to create a 3D object. The object is then heated to bond the layers together, creating a strong, lightweight part.
Cubicure
Cubicure is a Vienna-based company that specializes in the field of 3D printing technologies. The company was spun off from the Vienna University of Technology in 2015 and has been innovating in the additive manufacturing industry ever since.
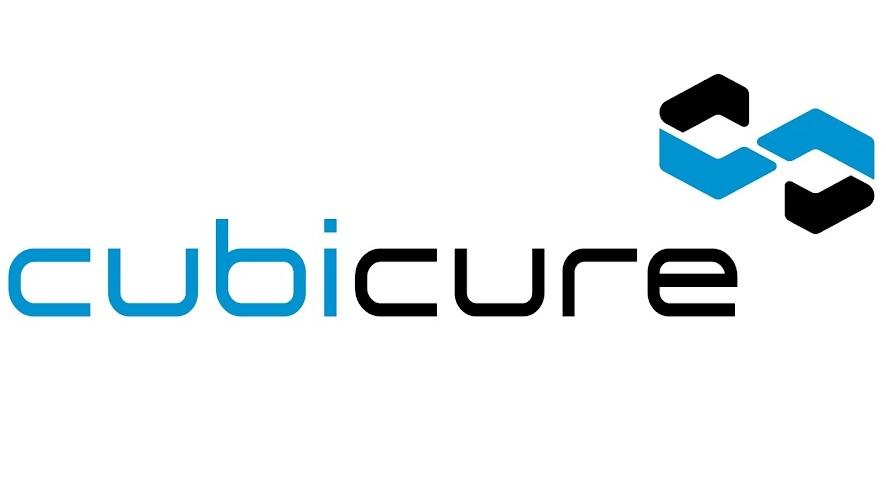
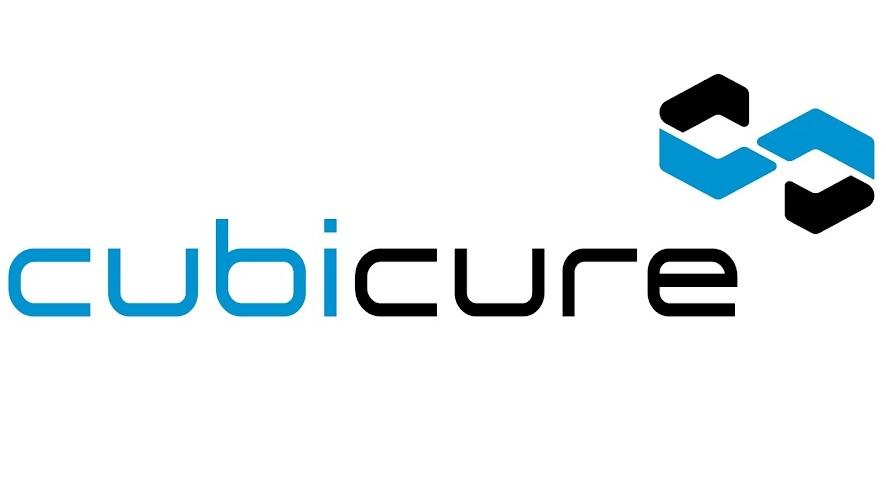
Cubicure’s core technology revolves around the photopolymerization of resins, a process known as Stereolithography (SLA). However, they have made notable advancements in this field with their patented Hot Lithography technology. This unique approach involves heating the resin before curing it, resulting in parts with higher dimensional stability and mechanical properties.
The company offers a variety of 3D printers and a wide range of resins that cater to different applications. Their Caligma 200, for instance, is a high-precision 3D printer designed for industrial use. Cubicure’s products serve a wide range of industries, from medical and dental to automotive and aerospace.
While Cubicure does not directly work with sheet lamination techniques, its contributions to the 3D printing industry through resin-based technologies are significant and worth noting.
Impossible Objects
Innovative business Impossible Objects is situated in Northbrook, Illinois, in the United States. The business was established in 2009 with the intention of transforming the additive manufacturing industry.
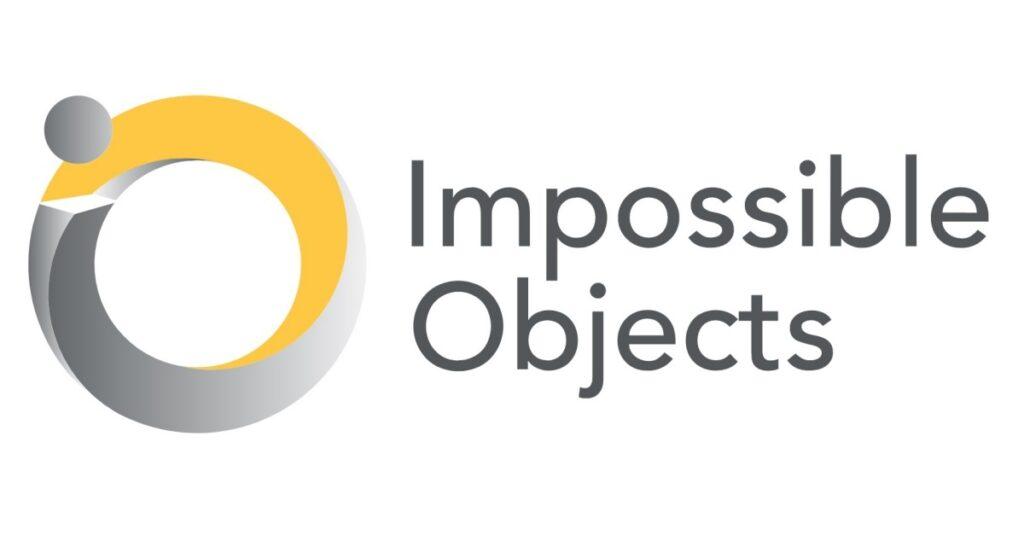
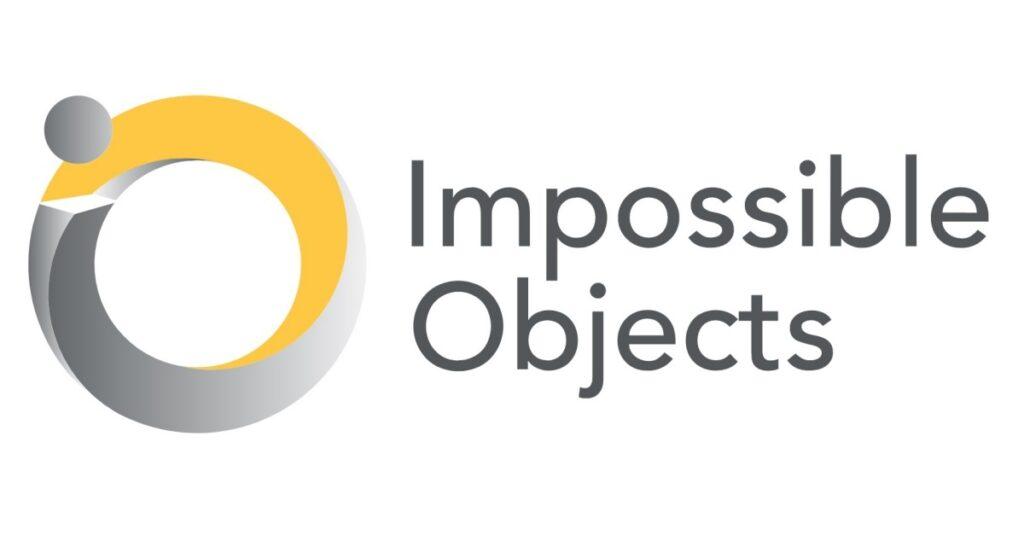
The company’s proprietary 3D printing method, known as Composite-Based Additive Manufacturing (CBAM), combines the advantages of additive manufacturing with the advantages of composite materials. Parts can be produced using this approach that is both lighter and stronger than those made using conventional manufacturing techniques.
The CBAM process is novel because it actively employs sheets of composite materials like carbon fiber, Kevlar, or fiberglass. These sheets undergo selective printing with a polymer binder to assume the shape of the desired item. The process then stacks, compresses, and heats the layers to fuse them together. After removing the extra material, it produces a highly resilient, lightweight component that various industries can use.
The technology of Impossible Objects has received praise for its originality and potential influence on the industrial sector. The company’s Model One and Model 2 printers can mass-produce high-performance parts and are intended for industrial applications.
Impossible Objects uses a technology that is a form of sheet lamination even if they don’t use the phrase “sheet lamination” to describe their procedure. They stand apart in the 3D printing sector thanks to their distinctive strategy.
Commercially Available Sheet Lamination Machines in the Market
Cubicure’s Hot Lithography systems: These machines use a unique method of stereolithography, which is technically not sheet lamination, but it’s worth mentioning due to Cubicure’s significant contributions to the field of 3D printing. Their Evolution and Evolve machines are known for high precision and versatility, capable of processing a broad range of materials.
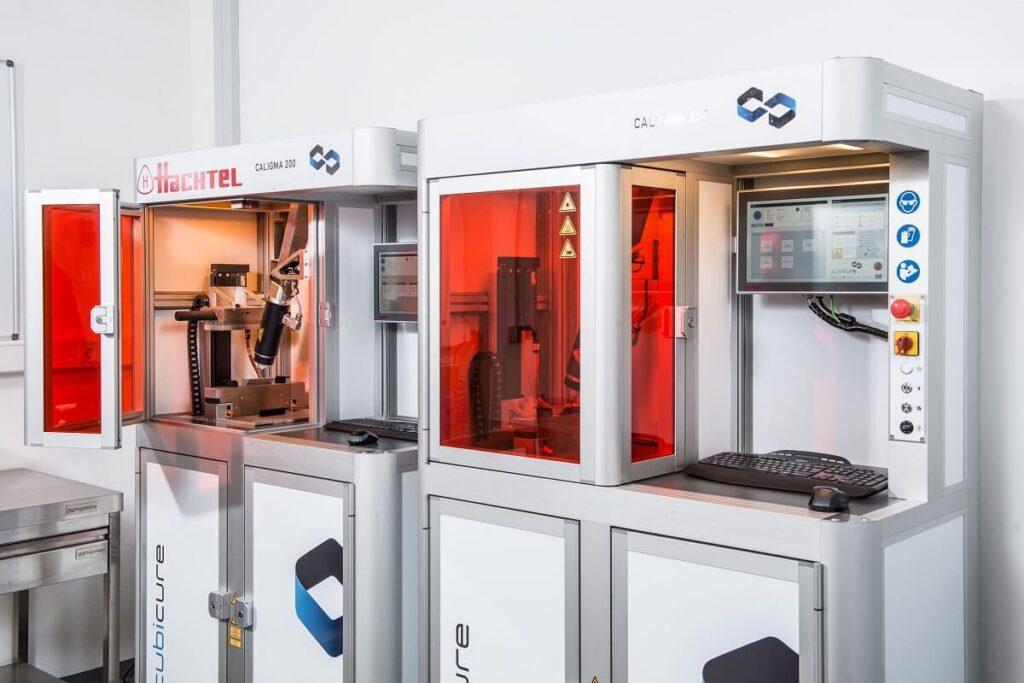
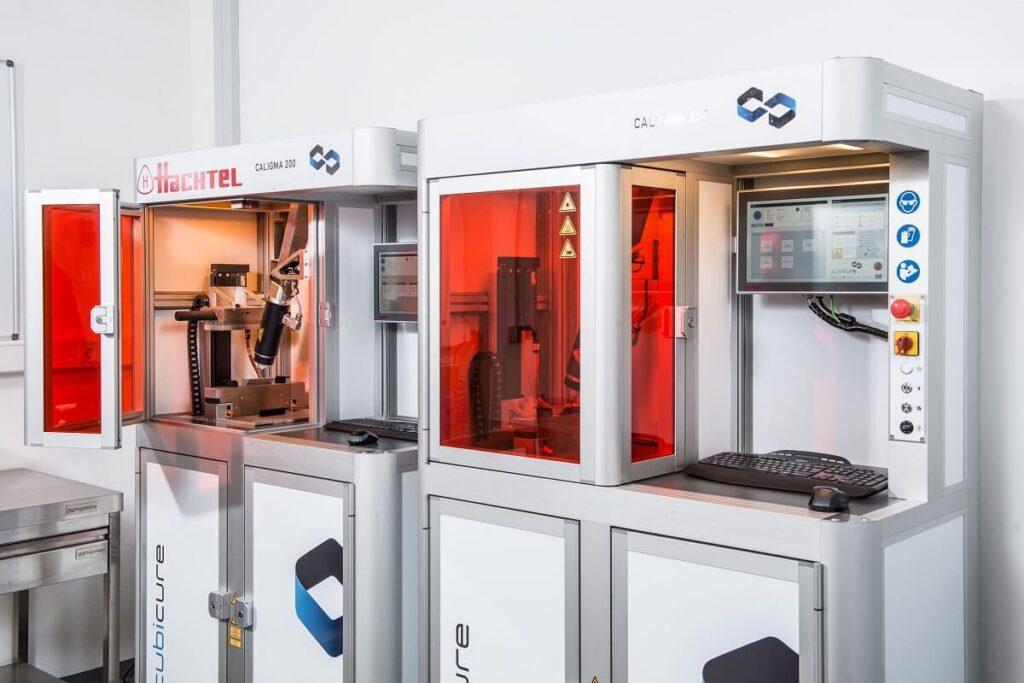
Impossible Objects’ Model One and Model Two printers: These use a process called Composite-Based Additive Manufacturing (CBAM), which involves laminating sheets of material together, similar to the process of sheet lamination. They are known for their ability to create parts that are both lightweight and strong, using materials like carbon fiber, fiberglass, and Kevlar.
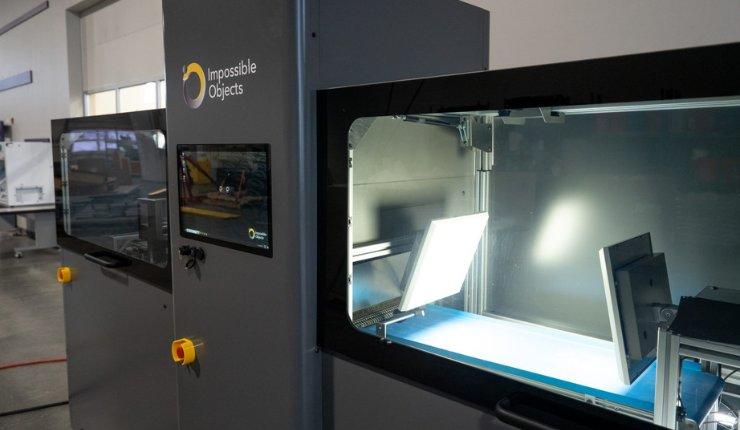
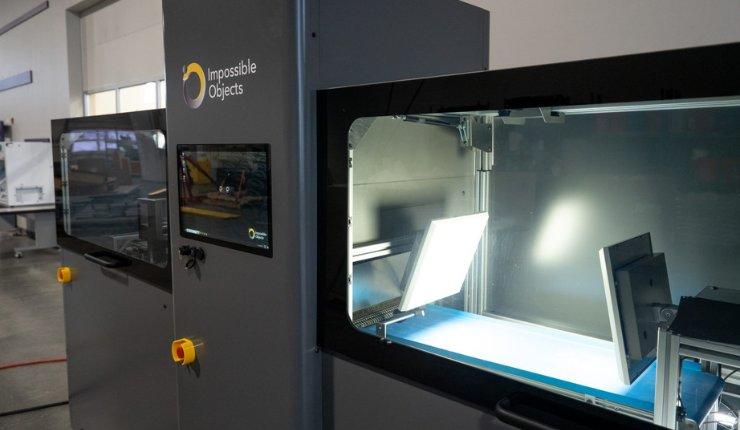
Conclusion
In conclusion, sheet lamination is a growing and creative industry, especially in 3D printing. Although this technology may not be as common as others like FDM or SLS, it has a lot of room for development. The employment of commonplace materials like paper in conjunction with cutting-edge methods may result in a more cost-effective and widely available manufacturing process. These innovations are being led by businesses like Cubicure and Impossible Objects, who are pushing the limits of what is practical in this area. We may anticipate additional advancements and breakthroughs as time goes on, which will help the 3D printing sector as a whole.
How to optimize the sheet lamination process for better results?
- Material Selection
Carefully select the lamination material. Different materials respond differently to lamination, affecting the final product’s quality.
- Machine Calibration
Ensure your machine is properly calibrated. This includes checking the temperature settings, alignment, and pressure controls.
- Preparation of Sheets
Properly prepare and align the sheets to be laminated. Any misalignment can lead to errors in the final product.
- Optimize Speed
Adjust the speed of lamination. A slower speed may improve the adhesion between layers, enhancing the final product’s quality.
- Monitor the Lamination Process
Regularly monitor the lamination process. This can help you quickly identify and address any issues that may arise.
- Post-Lamination Quality Check
After lamination, perform a quality check. This may involve inspecting the final product for any defects and testing its durability.
- Regular Maintenance
Maintain your lamination machine regularly. A well-maintained machine will consistently produce better-quality laminations.
- Continuous Improvement
Continuously review and improve your lamination process based on the feedback and results from previous laminations.
FAQs
The sheet lamination process can be used with various materials such as paper, plastic, or metal sheets. The choice of material can greatly impact the final product’s quality and characteristics.
The primary advantage of sheet lamination is its ability to create parts with excellent mechanical properties and dimensional accuracy. Moreover, it can be more cost-effective when working with paper or certain types of plastic materials.
Some challenges in sheet lamination include the limitation of materials that can be used, the difficulty of removing support structures, and the necessity for a controlled environment to prevent material distortion.
While sheet lamination can be used for small to medium-sized production, it might not be the most efficient for large-scale manufacturing due to the time-consuming nature of the process.
Quality can be improved by careful calibration of the machine, proper preparation of the sheets, optimal speed settings, and regular monitoring of the lamination process.