Material Jetting: Everything You Need
Material Jetting (MJ) is a type of additive manufacturing that works similarly to 2D printers. A printhead (similar to those used in standard inkjet printing) sprays droplets of a photosensitive substance that solidifies under ultraviolet (UV) light, layer by layer, to form a component. The thermoset photopolymers (acrylics) utilized in MJ are liquid.
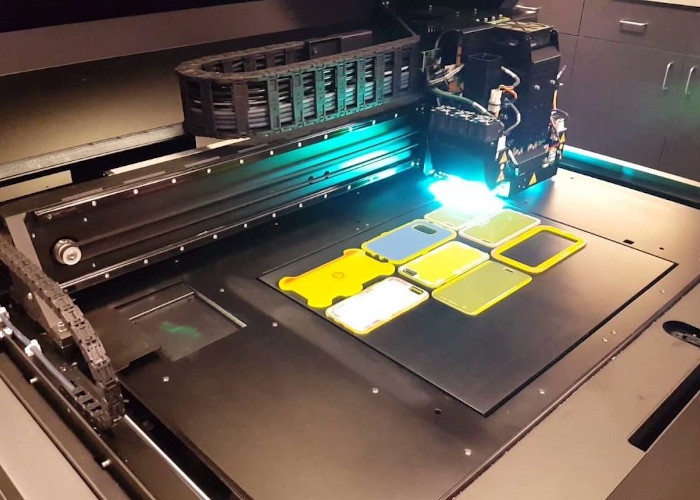
What is Material Jetting?
Material jetting (MJ) is a very efficient and accurate method of 3D printing. This printer uses UV light to transform liquid photopolymers into solid pieces.
It frequently likened MJ to the 2D inkjet method since it sprayed the photopolymer resin in droplets before solidification. On the other hand, MJ builds layer upon layer until the component is complete, whereas inkjet printers deposit a single layer of ink droplets.
Because it employs a UV light source to cure the resin, MJ is comparable to SLA. The distinction here is that MJ 3D printers spray hundreds of tiny droplets simultaneously, whereas SLA 3D printers contain a whole vat of resin selectively cured by a laser (point-wise).
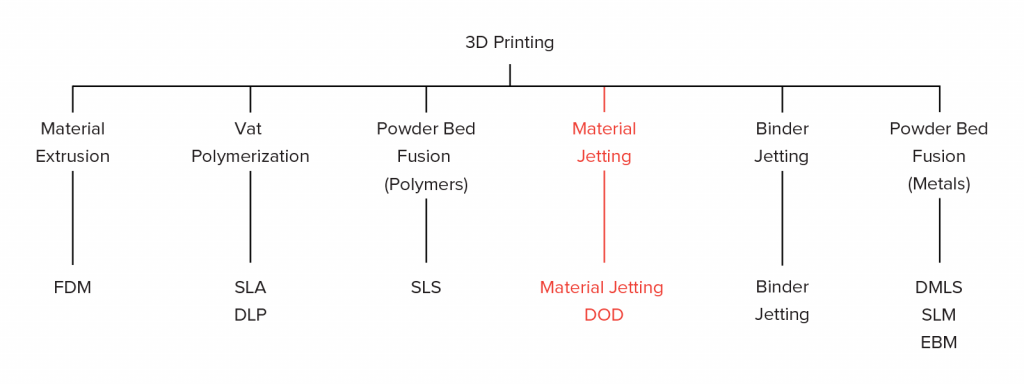
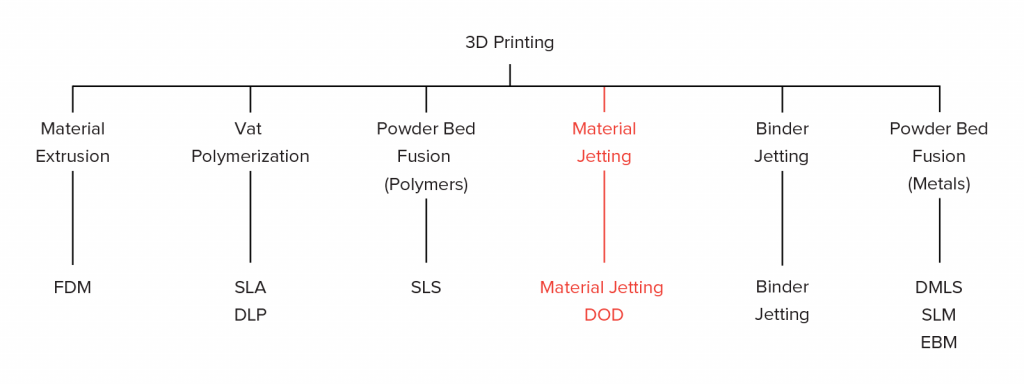
MJ 3D Printing produces high-dimensionally accurate parts with a flawless surface finish. Material Jetting offers multi-material printing and a wide choice of materials (including ABS-like, rubber-like, and transparent materials). These features make MJ an appealing option for visual prototypes and tooling production. Nonetheless, material jetting has certain significant drawbacks, which we discuss in this essay.
A version of the MJ process uses Drop-On-Demand (DOD) printheads to distribute viscous liquids and generate wax-like parts. Thus, DOD has become less commonly used than other methods of investment casting.
material jaetting history
Objet Geometries, an Israeli 3D printer firm, invented material jetting in Rehovot in 1998. Rami Bonen, Gershon Miller, and Hanan Gotaait developed the technique. Objet Ltd, a firm, patented Material Jetting (MJ) in 1999. Stratasys bought PolyJet in 2012, The endeavor was a success, and by 2000, the business had secured a $15 million investment, valuing it at $36 million. Objet and Stratasys announced a merger in April 2012 to combine the printer portfolios of both 3D printer businesses. PolyJet 3D printers are now available from Stratasys as part of their product line.
How does material jetting work?
Printing with resin is a two-step process. First, you must heat the liquid material to between 30 and 60 degrees Celsius to make it more viscous. The printhead then moves across the build platform, jetting/depositing hundreds of microscopic droplets of photopolymer to the desired spots. A UV light source connected to the printer cures the deposited material, hardening it and forming the first layer of the component. The building platform goes down one layer height, and then the process repeats until it completes the entire portion.
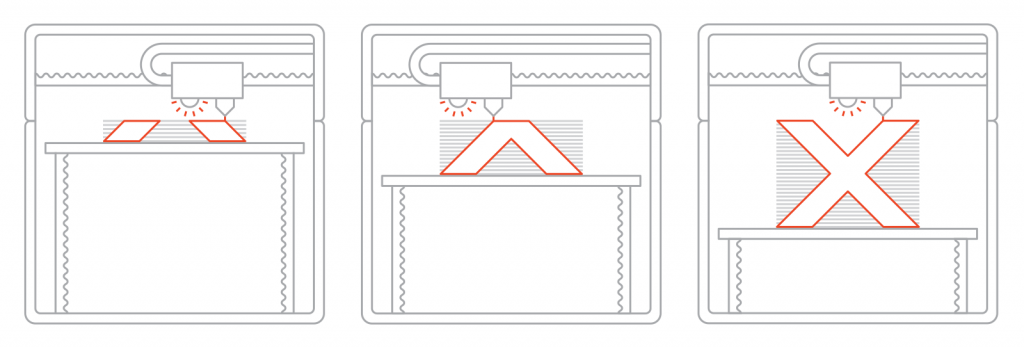
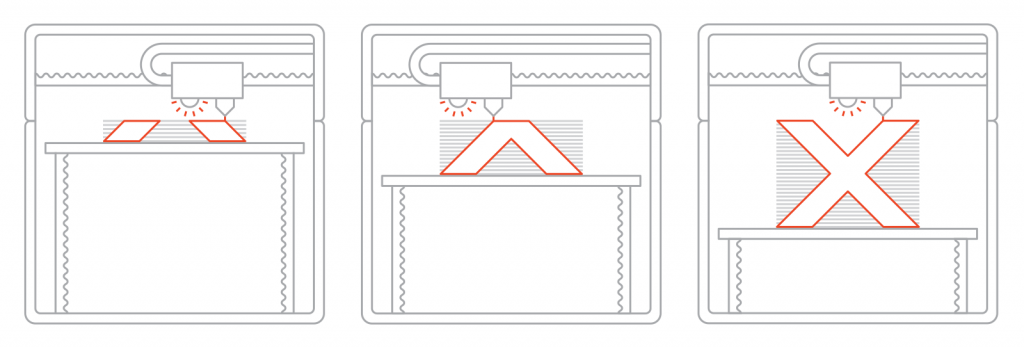
MJ deposits material in a line-by-line method, unlike most other 3D printing processes. They mount multiple inkjet printheads side by side on the same carrier and deposit material across the whole print surface in one pass. Because multiple heads may dispense different materials, multi-material printing, full-color printing, and the dispensing of dissolvable support structures are familiar and straightforward. Material jetting requires support structures, and we must remove them afterward.
A process known as photopolymerization solidifies the liquid substance in Material Jetting. Photopolymerization Using material jetted parts have uniform mechanical and thermal characteristics, similar to SLA. Still, unlike SLA, they do not require extra post-curing to attain their ideal qualities because of the relatively low layer height utilized.
Material Jetting Materials
Material Jetting employs thermoset photopolymer resins with features and restrictions comparable to those used in SLA (they are brittle, have a low heat deflection temperature, and are susceptible to creep). They are less viscous, ink-like, and cost substantially more per kilogram (about $300 – $1000).
MJ’s multi-material printing capability allows for precise visual and tactile prototypes. Specialty materials for specific sectors, such as tooling (injection molding, thermoforming, etc.) and medicinal uses, are also available.
The most common materials used in material jetting are photopolymers and casting wax.
material Jetting companies
3D Systems and Stratasys are two of the most well-known material Jetting companies on the market, with a wide choice of photo-curable polymers and composites to choose from. For example, Stratasys has recently produced “digital materials” in its patented PolyJet technology.
They make these materials up of two or more photopolymers, resulting in a hybrid material (e.g., combining rigidity with flexibility). Although such materials are weak and brittle, some are very good for specific uses such as tooling and investment casting.
Metals, ceramics, and silicones have already begun to reach the market due to extensive research into broadening the variety of materials employed with material jetting.
For example, the Israeli business Xjet has developed NanoParticle Jetting technology for metals and ceramics. We suspend ceramic, or metal particles in a liquid formulation with this method subsequently removed during the sintering stage.
Silicone 3D printing
Silicone 3D printing, created by ACEO®, a part of the German chemical giant Wacker Chemie AG, has set a new standard in materials for Material Jetting. ACEOtechnology, whose first announcement was in 2016, employs a “drop-on-demand” process to make 100% silicone parts and multi-material parts with varying colors and hardness.
advantages and disadvantages
MJ 3D printing, like any other 3D printing method, has advantages and disadvantages.
advantages
As previously stated, the two criteria that set MJ apart are build speed and dimensional accuracy.
The nature of the technology makes it possible to produce numerous parts without reducing the build speed, which is already quick for a single part. This possibility is beneficial for shared or small-scale production.
Parts created with MJ have an exceptionally smooth surface, making them suitable for aesthetic prototypes. So much so that we can compare injection-molded parts to material jetted parts (in terms of looks).
Another fantastic feature of MJ is full color and multi-material 3D printing, which improves the visual quality of both prototypes and end-use parts.
disadvantages
A premium price tag comes with high-performance printing and an exceedingly smooth surface finish. One of the most costly 3D printing methods is MJ because both the machinery and the materials are expensive.
The strength of the printed parts is another MJ constraint. The structural weakness of MJ parts makes them unsuitable for use in structural components that must bear weight.
In reality, MJ and SLA both have this restriction. Because of the nature of the resin, parts produced using either process are delicate.
Finally, MJ does not come without its share of trash. MJ, like FDM and SLA, requires support for parts with overhangs. Any waste is unwelcome because of the expensive cost of resins — even dissolvable support material.
APPLICATIONS FOR MATERIAL JETTING
As you may have predicted, MJ is mainly used to create gorgeous, realistic-looking prototypes.
Doctors and students, for example, could be interested in MJ’s exact representations of bodily parts. Similarly, material jetted models’ precision and visual quality may significantly aid architects, designers, and artists.
Because of its incredible detail and thermal stability, MJ may also build low-volume injection molds.
In any event, the expense of 3D printing parts using MJ limits the technology’s use to professional applications in the vast majority of situations. Even if you can’t afford an MJ printer, you can still use a 3D printing service to get your ideas produced in high-detail resin.
Full-color prototypeds
PolyJet is the best way to make detailed visual prototypes because it can make smooth and full of color surfaces. This Full-color prototyping allows designers and engineers to see how their product looks in person, how it works, and how it looks. It’s used a lot to make mold patterns that we can use for other things, like making injection molds. PolyJet is used to make the original prototype, which we use to make a lot of injection molded products.
Realistic models for education
Another everyday use of Material Jetting 3D printing is to make realistic models, like anatomical models of human organs. These models can then help students learn how to do medical procedures to have more experience before they do actual surgeries. This shortening of the learning curve significantly reduces the number of people who die during surgery.
differences between PolyJet and Material Jetting
PolyJetting and Material Jetting are two terms for the same technology. Object Geometries patented the name PolyJet in the late 1990s, whereas Material Jetting is the technical term for the method. Fused Deposition Modeling is also known as Fused Filament Fabrication: one is a patented ‘brand’ term, and the other is a technical name. Throughout this guide, we’ll use both words interchangeably.
PolyJet has been used to 3D print the parts. We will note complex geometries and fine surface finishes. You’ll need a 3D printer file, just as with any other technology. You’ll need to upload this file to a 3D slicer tool like Cura, usually an STL file. These applications will figure out how to print your item based on the layer sizes and print parameters you’ve chosen, such as infill %, layer thickness, and more.
Material Jetting vs SLA
Because PolyJet employs photopolymers similar to SLA, the two techniques are comparable. SLA 3D printers, on the other hand, employ far higher-heat vat polymerization processes than PolyJet, which uses lower temperatures (30-60C).
PolyJet 3D printers, like SLA 3D printers, employ a UV-cured liquid resin, but the similarities end there. PolyJet 3D printers employ an inkjet-like print head to disperse resin onto the print bed, rather than the dirty, stinky, and potentially dangerous pool of resin used in SLA machines.
This printing technology has several benefits over SLA 3D printing. Break-away support material is the only material that SLA 3D printers can utilize because they only use one material at a time. PolyJet printers employ a washable or soluble gel-like support substance to print exceedingly complex geometries and assemblies of parts.
It entirely cured poly jet parts as they leave the build platform with no liquid resin residue, avoiding the need for numerous alcohol baths or post-curing. Polyjet 3D printers can also make parts in large quantities faster than SLA machines.
Because this process employs soluble supports, Material Jetting would likely be more straightforward for the print service provider. Manually removing SLA supports (flush cutters) and sanding them down is required.
FDM Vs. Material jatting
PolyJet is more expensive and industrial, while Fused Deposition Modeling is the most economical and accessible 3D printing process. One significant distinction is that parts made with PolyJet are noticeably weaker than those made with an FDM 3D printer. They deteriorate in strength over time, whereas FDM parts maintain their strength and shape. On the other hand, Material Jetting is faster, has more material and color possibilities, and is scalable.
A thermoplastic filament is melted and extruded from a print head in FDM. The material is quickly set at the machine’s high temperatures and laid on a platform after being extruded into a bead. Layer by layer, the machine head continues the extrusion and melting until the component is complete.
In the PolyJet method, a carriage sprays photopolymers onto the work surface, subsequently cured by UV light. Following the creation of a thin layer, the procedure is repeated by jetting more layers until it entirely produces the component.
Because the processes and materials are diverse, the qualities of the parts produced by each will change. When it comes to selecting the right technology, there are a few aspects to keep in mind:
Details
While PolyJet is known for its attention to detail, FDM is known for its capacity to generate long-lasting parts that are ready for use. If your part’s fit and function are crucial, FDM may be the best option.
kind of material
It’s also crucial to think about what kind of material you’ll need for your part’s application. PolyJet will manufacture the little features and fine textures you want if attention to detail is a critical component of your product. PolyJet can also print parts with varying degrees of flexibility, ranging from rubber-like to more hard.
When printing in FDM, you may pick from several thermoplastics that can endure a broad range of conditions, from severe temperatures to chemical exposure.
Surface quality
The value of how a part appears after it’s finished is primarily determined by how we will use it. Surface quality and aesthetics are essential for concept models and specific prototypes. PolyJet’s utilization of different materials and attention to detail is frequently a viable option in this instance.
FDM can nevertheless generate parts with complicated geometries and intricate components, even if it lacks the intricacy of PolyJet. Layer lines are produced by the FDM process on parts, although these lines usually have little effect on the strength or functioning of the item.
size
When selecting a technique, we must also consider the size of the part. PolyJet and FDM have comparable maximum part sizes for a single system: PolyJet parts can be up to 39.3 x 31.4 x 19.6 in., while FDM parts may be up to 36 x 24 x 36 inches.
On the other hand, FDM technology lets you make parts as large as you need them to be. Suppose your item is more significant than the FDM dimensions shown above. It might be possible to break the design file into many parts, each of which can be made on its machine and then glued together to make a single part.
Both technologies have advantages and disadvantages; ultimately, the application of the part will determine which technique is employed. PolyJet is a beautiful alternative if you need high-resolution, ultra-fine parts. On the other hand, FDM is your best alternative if durability and end-use function in harsh circumstances are vital to you.
Material Jetting Post-Processing
It takes more material to make PolyJet supports than to make FDM or SLA ones. Material Jetting can be very pricey. Using more support adds to its cost, But it’s straightforward to get rid of them since it made them of things that disintegrate when they come into contact with water.
The parts don’t warp or shrink during the printing process because we don’t use extreme heat. This topic shows that PolyJet is one of the most accurate and best surface finishes of all the 3D printers. However, large parts can get out of shape because the resins will shrink as they dry. So, consider using other technologies, like Binder Jetting, for significant parts. It’s essential to be careful when handling parts because they can warp when exposed to hot or wet weather.
Though PolyJet has the best surface finishes of all the technologies that can make things, there are still many ways to finish them after it has made them. When you coat the part, you might want to sand it down before doing anything else. Also, parts can be dyed and painted to change their color. However, this isn’t always necessary because you can print in full bloom.
precise 3D printing technologies
PolyJet is one of the most precise 3D printing technologies, capable of producing incredibly smooth finishes with the precision of up to 16 microns. Two characteristics of Material Jetting: jet droplet size (equivalent to laser spot size in SLA) and layer height. highly influenced the part quality
We may use material Jetting on a wide range of materials and colors. PolyJet allows you to use Material Jetting to generate multi-colored or even full-color 3D printer parts and print parts with many distinct materials in various portions of the part! PolyJet printers, like high-quality 2D inkjet printers, can produce a nearly limitless range of colors since they’re compatible with Pantone color ranges.
Various print heads, such as those used in twin extruder FDM 3D printers, enable the creation of various materials simultaneously. The creation of Multi Jet Fusion 3D printing appears to have been motivated by Material Jetting’s success in full-color printing.
Refrence
- https://www.hubs.com/knowledge-base/introduction-material-jetting-3d-printing/
- https://additive-manufacturing-report.com/technology/polymer/material-jetting/
- https://all3dp.com/2/what-is-material-jetting-3d-printing-simply-explained/
- https://amfg.ai/2018/06/29/material-jetting-3d-printing-guide
- https://www.3dsourced.com/guides/polyjet
- https://www.cadimensions.com/blog/sla-vs-polyjet-need-know/
- https://www.hubs.com/talk/t/sla-vs-material-jetting/11821/3
- https://www.stratasysdirect.com/manufacturing-services/3d-printing/fdm-vs-polyjet-tale-of-two-3d-printing-technologies