Introduction to Additive Manufacturing (AM)
What is Additive Manufacturing (AM)? Additive manufacturing, also known as 3D printing, is a revolutionary manufacturing process that transforms digital designs into physical objects. By layering successive materials, it creates three-dimensional products directly from a digital file. This emerging technology has the potential to transform various industries and revolutionize traditional manufacturing methods.
In its infancy, additive manufacturing has already showcased remarkable applications in fields such as medicine and aerospace. The ability to produce complex geometries and intricate designs has made it valuable in producing medical devices and components for the aerospace industry. However, the scope of additive manufacturing extends far beyond these sectors, and its impact is anticipated to expand into areas such as consumer goods, automotive manufacturing, and even surgical procedures.
With additive manufacturing, the conventional limitations of subtractive manufacturing processes are overcome. Instead of starting with a solid block of material and removing excess material to shape the object (subtractive manufacturing), additive manufacturing builds the object layer by layer. This approach allows for greater design freedom, reduced material waste, and the ability to create highly customized and intricate structures.
The potential benefits of additive manufacturing are vast. It offers improved production efficiency, reduced lead times, cost savings, and the ability to create complex geometries that were previously unattainable. However, like any technology, it also comes with its own set of challenges and considerations.
As the world embraces additive manufacturing, it becomes essential to understand its various aspects, from the underlying processes and materials to the potential applications and impacts on different industries. In the following sections, we will explore the fundamental concepts, processes, applications, and considerations associated with additive manufacturing.
Understanding Additive Manufacturing (AM)
Additive manufacturing or AM, also known as 3D printing, has gained significant attention in recent years due to its potential in revolutionizing manufacturing processes. Despite its increasing popularity, there are still misconceptions surrounding AM, such as its perceived high cost and requirement for specialized expertise. However, with advancements in technology and accessibility, additive manufacturing is gradually making its way into mainstream manufacturing.
So, what exactly is AM and why is it useful? Imagine seeing a beautifully crafted piece of jewelry, an intricately designed cup, or a complex machine part, and wondering about the precise manufacturing process behind it. In this article, we will explore additive manufacturing (AM) and provide answers to your questions. You’ll discover what AM is, how it can enhance your products or services, and potentially save you money in certain cases.
Additive manufacturing involves building three-dimensional objects by layering materials on top of one another, in contrast to traditional subtractive processes like casting, forging, turning, and milling. As the advantages of additive manufacturing become more evident, its adoption in industrial applications continues to increase.
The Power of 3D Printing
3D printing, a key aspect of additive manufacturing, holds immense potential in creating unique and customized products. It offers an excellent alternative for individuals seeking to produce one-of-a-kind items or searching for alternatives to mass-produced brands. If you’re unsure about which 3D printer suits your needs, this guide will assist you in finding the right one.
Rapid Prototyping
Rapid prototyping refers to a set of techniques used to quickly produce scaled models of physical parts or assemblies for testing purposes, utilizing three-dimensional computer-aided design (CAD) data. Additive layer manufacturing, also known as 3D printing, has become a standard method for creating prototypes and assembly components.
The origins of rapid prototyping can be traced back to the mid-1980s when the first accessible technologies emerged. Initially, they were employed for creating models and prototype parts across various applications. Nowadays, they find use in a wide range of industries, enabling the production of small quantities of production-quality components economically and without the constraints associated with traditional manufacturing methods.
How Does Additive Manufacturing Work?
Additive manufacturing involves creating three-dimensional objects by layering small pieces of material on top of each other. This process is facilitated by digitally defined objects through computer-aided design (CAD) software. The digital design is “sliced” into ultra-thin layers using STL files, guiding the direction of a nozzle or print head to accurately distribute the material onto the preceding layer. Another approach involves selectively melting or partially melting a bed of powdered material using a laser or electron beam. The subsequent cooling or curing process fuses the materials together,
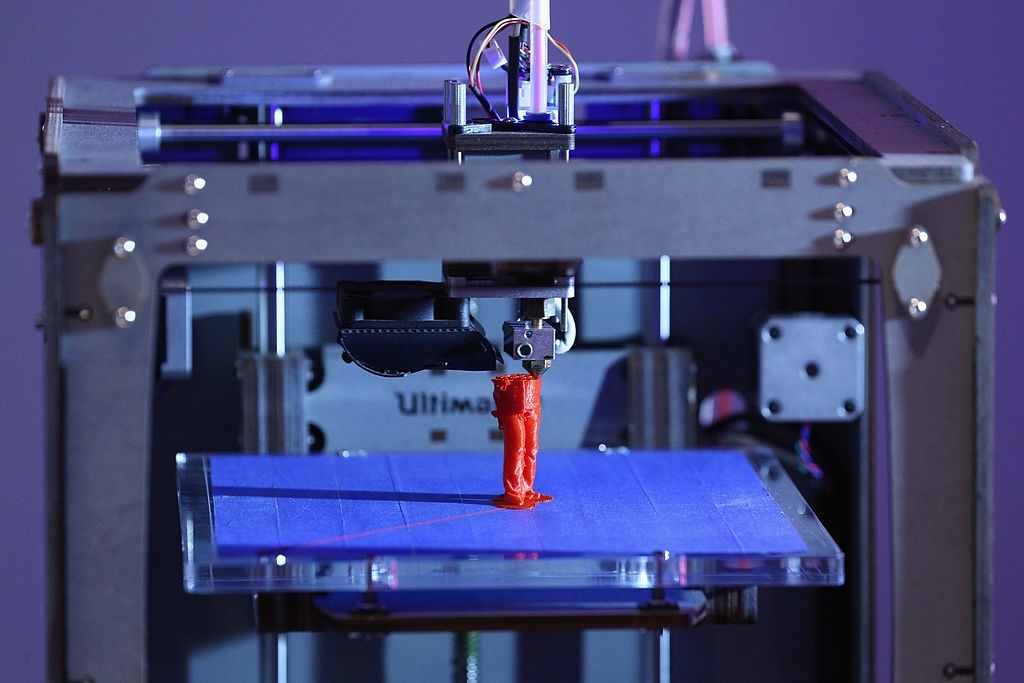
What is Additive Manufacturing (AM)?
Additive manufacturing (AM) is 3D printing for industrial production, creating objects by depositing materials layer by layer. AM adds material layer by layer, unlike subtractive manufacturing which removes material. AM builds geometries by adding feedstock like filament, wire, or powder, instead of removing material.
A Brief History of AM
Additive manufacturing has roots that date back several decades. Key milestones shaped its development and eventual emergence. It has become a revolutionary manufacturing process. Here is a brief history of AM.
The 1950s-1980s: The Birth of Additive Manufacturing
Additive manufacturing can be attributed to the efforts of various pioneers during this period. In the 1950s, the concept of layer-by-layer manufacturing was first explored through the development of numerical control (NC) systems. In the 1970s, researchers started experimenting with additive processes. One method was stereolithography, which cured liquid photopolymers layer by layer. They used UV light to selectively cure the photopolymers and create the desired object.
1980s-1990s: Advancements and Commercialization
The 1980s marked significant advancements in additive manufacturing techniques. In 1984, Charles Hull invented stereolithography, which led to the commercialization of 3D printing technology. In the 1990s, SLS and FDM processes expanded additive manufacturing possibilities.
The 2000s-2010s: Widening Applications and Accessibility
The 21st century witnessed rapid growth in the adoption of additive manufacturing. It began to find applications in various industries, including aerospace, automotive, healthcare, and consumer products. During this time, new materials and technologies were introduced, allowing for improved accuracy, speed, and versatility in the production of complex geometries.
Present and Future: Advancements and Integration
Additive manufacturing continues to evolve, with ongoing advancements in materials, processes, and equipment. Metal 3D printing has gained prominence, enabling the production of functional and high-performance metal parts. The integration of additive manufacturing with other technologies, such as robotics and artificial intelligence, further expands its capabilities.
Today, additive manufacturing is on the cusp of widespread adoption and is poised to revolutionize traditional manufacturing methods. As technology becomes more accessible and materials continue to advance, it holds the potential to transform industries, unlock new design possibilities, and reshape the future of manufacturing.
This brief history showcases the transformative journey of additive manufacturing, from its early conceptualization to its current state as a disruptive force in the manufacturing landscape.
Additive Manufacturing vs. Subtractive Manufacturing
Additive Manufacturing and Subtractive Manufacturing are two distinct approaches to manufacturing processes that differ in their methodology and applications. Let’s explore the differences between these two methods:
Additive Manufacturing
Additive Manufacturing, as explained earlier in this post, involves the use of additives to create products. It is commonly associated with 3D printing, where materials are layered on top of each other to build a complete object or part. This process starts with a digital design created using computer-aided design (CAD) software. The chosen additive manufacturing method, such as material deposition or powder fusion, is then employed to fabricate the part. Post-processing steps, like polishing and finishing, may be required before the part is ready for use.
Subtractive Manufacturing
On the other hand, Subtractive Manufacturing involves the machining and material removal processes used on various materials, including metals, solid blocks, and bars. Cutting, drilling, milling, and grinding are some of the techniques used to remove material from a workpiece. Computer numerical control (CNC) machines are commonly utilized in subtractive manufacturing. CAD software generates a virtual model. The software simulates tool paths. Tool paths guide cutting tools. Cutting tools perform necessary removals. Removals include creating holes, and channels, and shaping the part.
Distinguishing Factors
- Methodology: Additive Manufacturing builds objects layer by layer, while Subtractive Manufacturing removes material from a solid block or workpiece.
- Design Flexibility: Additive Manufacturing offers greater design freedom and the ability to create complex geometries that may be challenging or impossible with Subtractive Manufacturing.
- Material Waste: Additive Manufacturing typically generates less waste since it adds material precisely where needed, whereas Subtractive Manufacturing can result in significant material waste due to the removal process.
- Prototyping vs. Production: Additive Manufacturing is often favored for rapid prototyping and small-scale production, enabling the creation of custom or low-volume parts. Subtractive Manufacturing is commonly used for larger-scale production and machining operations.
- Time and Cost: Additive Manufacturing can be time-consuming, especially for complex parts, while Subtractive Manufacturing may be faster for simpler designs. The cost considerations vary depending on factors such as material usage, machine capabilities, and production volume.
Understanding the differences helps manufacturers choose the right approach for their requirements. Considerations include design complexity, production volume, and cost. Additive Manufacturing and Subtractive Manufacturing are the two approaches to consider. Manufacturers can select the most suitable method based on their specific needs. Both methods have unique advantages and play essential roles in modern manufacturing processes.
Pros and Cons of Additive Manufacturing (AM)
Additive Manufacturing (AM) offers a range of benefits and drawbacks that should be considered when implementing this technology. Here are the pros and cons of AM:
Pros:
- Design Flexibility: AM allows for intricate and complex designs, enabling the production of customized and highly intricate parts that may be challenging or impossible to create with traditional manufacturing methods.
- Reduced Material Waste: AM adds material precisely where needed, minimizing waste compared to subtractive manufacturing methods that often generate significant material waste.
- Rapid Prototyping and Iteration: AM enables quick and cost-effective prototyping, allowing for faster product development cycles, iterations, and design improvements.
- Assembly Consolidation: AM can consolidate multiple components into a single complex part, reducing the need for assembly and improving overall part strength and integrity.
- Lightweighting and Material Optimization: With AM, intricate lattice structures and internal cavities can be created, reducing weight while maintaining structural integrity. This opens up possibilities for material optimization and efficient use of resources.
- On-Demand Manufacturing: AM enables on-demand production, allowing for the production of parts as needed, reducing inventory costs, and enabling just-in-time manufacturing.
- Customization and Personalization: AM facilitates the creation of customized products tailored to specific individual requirements or niche markets.
Cons:
- Production Speed: Compared to traditional manufacturing methods, additive manufacturing (AM) can be slower, especially for large or complex parts, which limits its suitability for high-volume production.
- Limited Material Selection: Although the range of available materials for AM is expanding, it may not offer the same variety and properties as traditional manufacturing materials, limiting certain applications.
- Equipment and Infrastructure Costs: The initial investment in AM equipment, such as 3D printers and associated software, can be relatively high, making it a significant upfront cost for businesses.
- Post-Processing Requirements: Parts produced through AM often require post-processing steps like finishing, polishing, or additional treatments to achieve desired surface quality, which can add time and cost.
- Quality Control and Certification: Ensuring consistent quality and meeting industry standards and certifications can be challenging in AM due to the intricacies of the layer-by-layer manufacturing process.
- Lack of Scalability: Although low-volume production and customized parts are suitable for AM, the scalability of high-volume production can face limitations due to factors such as production speed, material availability, and cost-effectiveness.
- Design and Process Complexity: AM requires expertise in digital design, materials, and machine operation, making it essential to have trained personnel to ensure successful implementation.
Understanding the pros and cons of AM allows businesses to evaluate its suitability for their specific applications, balancing the benefits with potential limitations and considering factors such as production requirements, cost considerations, and desired design outcomes.
Additive Manufacturing Processes
Additive Manufacturing (AM) encompasses various processes that enable the creation of three-dimensional objects. Here are the seven primary additive manufacturing processes, each explained briefly:
1. Binder Jetting:
In Binder Jetting, the process selectively deposits a liquid binder onto a powdered material bed, layer by layer, to bind the particles together and form the desired shape.
2. Material Extrusion:
Material Extrusion, also known as Fused Filament Fabrication (FFF), involves the extrusion of a thermoplastic filament through a heated nozzle, which deposits the material layer by layer to build the object.
3. Powder Bed Fusion:
Powder Bed Fusion utilizes a laser or electron beam to selectively melt or sinter powdered materials, such as metal or polymer, layer by layer, to create fully dense parts.
4. Vat Polymerization:
In Vat Polymerization, a light source, such as a UV laser, selectively cures a liquid photopolymer resin layer by layer, solidifying the desired part.
5. Material Jetting:
In Material Jetting, multiple print heads deposit droplets of liquid photopolymer or wax material layer by layer, and then cure them to form the final object.
6. Directed Energy Deposition (DED):
DED utilizes focused thermal energy, such as a laser or electron beam, to melt and fuse metal or ceramic powders or wires, layer by layer, to build the part.
7. Sheet Lamination:
Sheet Lamination uses adhesive or heat to bond layers of sheet material together to form the object. The sheets may be paper, plastic, or metal.
Understanding the distinct characteristics of each additive manufacturing process allows for informed decision-making when selecting the most suitable approach for a specific manufacturing requirement.
Materials for Additive Manufacturing
Materials for Additive Manufacturing
Additive Manufacturing (AM) utilizes a wide range of materials to create three-dimensional objects. Here, we present a general overview of the materials that people commonly use in AM.
- Polymers/Thermoplastics: AM processes, such as Material Extrusion, commonly employ polymers like PLA and ABS, offering versatility and ease of use.
- Photopolymers: Vat Polymerization methods utilize liquid photopolymer resins that cure under light exposure, providing high detail and smooth surface finishes.
- Metals: Powder Bed Fusion and Directed Energy Deposition processes frequently utilize metal powders, such as aluminum, titanium, stainless steel, and cobalt-chrome alloys.
- Ceramics: In AM processes like Binder Jetting and Vat Polymerization, ceramics such as alumina, zirconia, and silicon carbide find use in applications that require high-temperature resistance or electrical insulation.
- Composites: Fiber-reinforced composites, combining materials like carbon fiber or glass fiber with polymers or resins, offer increased strength and stiffness in AM applications.
- Wax: Material Jetting and Binder Jetting processes can utilize wax-based materials for applications like investment casting or creating sacrificial patterns.
- Biochemicals/Biomaterials: In the medical field, practitioners have utilized additive manufacturing (AM) to create tissue-engineered constructs or customized medical devices using biocompatible materials such as bioresorbable polymers, hydrogels, or even living cells.
It’s important to note that the availability of materials may vary depending on the specific AM process and machine used. The continuous development of new materials expands the possibilities for AM and enables a wider range of applications in various industries.
The 3D printing process
Modeling
Before a manufacturing business can use a 3D printer to construct an object, the company must first create a product model using computer software. Making a model for 3D printing is the first stage in the process. Manufacturing companies utilize CAD software to build 3D object models. Once the product model is complete, it saves the model in one of two formats: stereolithography (STL) or additive manufacturing file (AMF).
Manufacturing businesses will verify the model file for faults throughout the modeling phase. During the modeling phase, Most CAD software can detect flaws that, if left uncorrected, might result in defects in the printed product. A model file that has holes, self-intersections, manifold weaknesses, and faces often does think of as a mistake because it doesn’t look right.
Printing
The second phase in 3D printing is the process of printing, or creating, the thing in three dimensions. Providing the STL or AMF file does not include any problems; the manufacturing business can send it to the 3D printer for printing. The 3D printer will follow the instructions in the matching file to determine where and how to put the material into the product.
Most 3D printers construct items by depositing layers of material onto a printing bed. The 3D printer will begin by creating the bottom layer, following which it will proceed to complete the next-highest layer. Three-dimensional (3D) printers can make products out of a variety of materials, with thermoplastic being the most frequently use. The printer head extrudes thermoplastic pellets or beads, which fall into the printing bed and mix to form the printed item.
Finishing
Finishing is the third and last phase in the 3D printing process. It is the process of applying the final touches to a printed piece, as the name implies. Finishing Adding solvents, for example, to a printed product may erase any superficial defects while also generating a smoother surface finish, which is beneficial in many situations. Other solutions, such as using employment supports to hold the object in place during printing, will require removal in the third and final step of the process.
A 3D printing project typically consists of three stages. It is necessary to first develop the object model using a computer-aided design (CAD) application. The third phase entails the construction of the item using a 3D printer. The third step is the finishing stage, which involves putting the finishing touches on the work.
AM Examples
In the pictures below, you can see some examples of additive manufacturing.
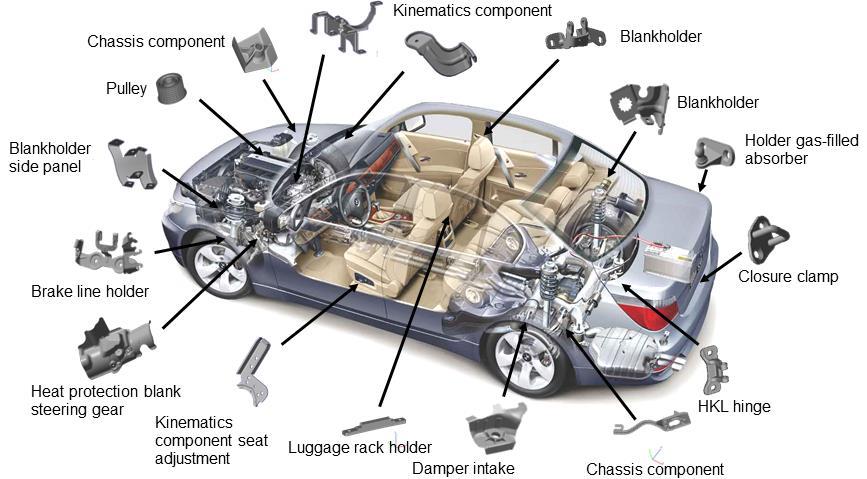
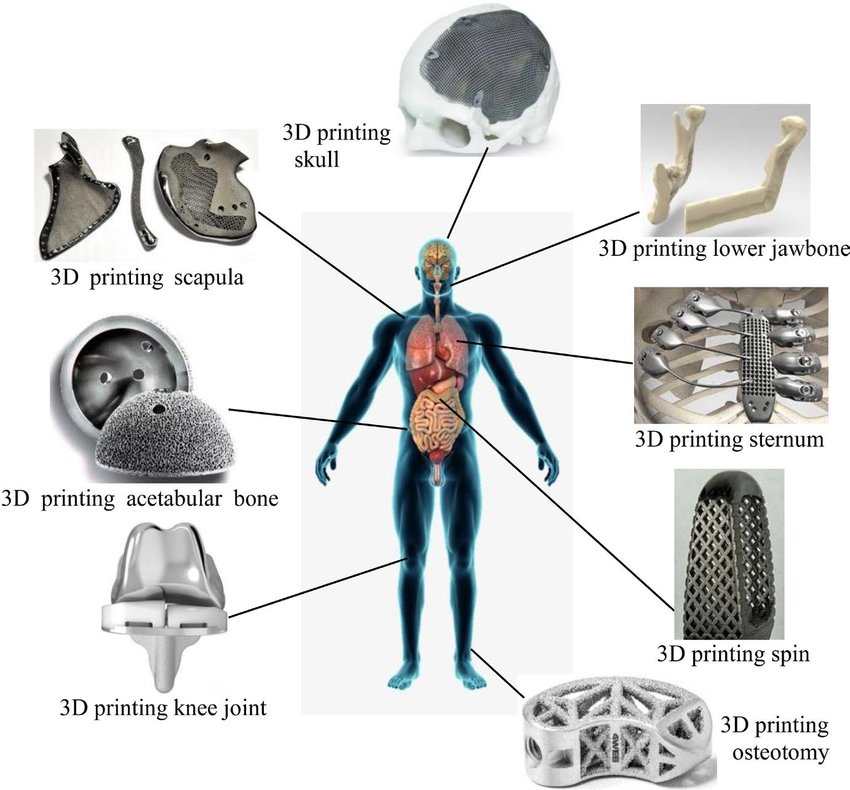
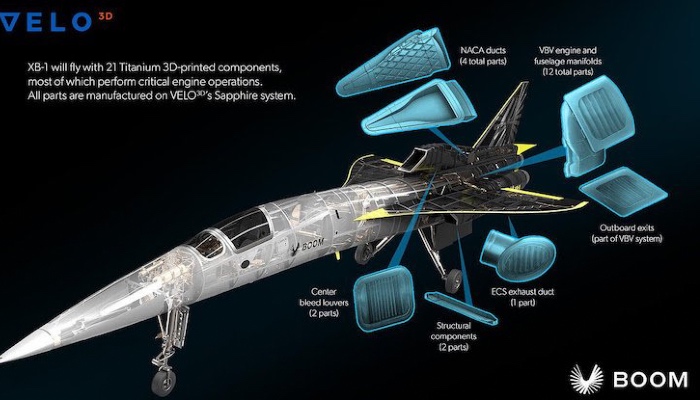
Conclusion
In conclusion, additive manufacturing, also known as 3D printing, is a transformative manufacturing process that creates three-dimensional objects by layering materials on top of each other. It offers numerous advantages, including design flexibility, reduced material waste, rapid prototyping, and the ability to create complex and customized geometries. Additive manufacturing has found applications in various industries, ranging from aerospace and automotive to healthcare and consumer goods.
While additive manufacturing presents many opportunities, it also has its limitations, such as production speed, material selection, and post-processing requirements. In addition, you should consider the initial costs of equipment and the requirement for expertise in digital design and machine operation.
Nevertheless, additive manufacturing continues to advance, with ongoing developments in materials, processes, and technologies. As it becomes more accessible and cost-effective, additive manufacturing is expected to revolutionize traditional manufacturing methods, offering new possibilities for design, production efficiency, and customization.
As the world embraces additive manufacturing, it is crucial to stay informed about its processes, materials, applications, and potential impacts on various industries. By understanding the principles and advancements of additive manufacturing, businesses can harness its power to innovate, optimize production, and unlock new opportunities in the manufacturing landscape.
How to Get Started with Additive Manufacturing?
- Understand the Basics
Learn about the principles and concepts of additive manufacturing. Familiarize yourself with different processes, materials, and applications to gain a solid foundation.
- Identify Your Goals
Define goals for additive manufacturing. Determine aims: rapid prototyping, customization, or production efficiency.
- Research and Select the Right Equipment
Explore additive manufacturing technologies and machines. Consider printing capabilities, build size, material compatibility, and budget to choose suitable equipment.
- Learn Design for Additive Manufacturing (DfAM)
Develop an understanding of Design for Additive Manufacturing (DfAM) principles. Learn how to optimize designs for additive processes, including considerations for support structures, layer adhesion, and part orientation.
- Acquire 3D Modeling Skills
Master 3D modeling software to create or modify digital designs for additive manufacturing. Practice and create accurate and precise models that you can easily translate into printable files.
- Choose the Right Materials
Research and select materials that are suitable for your desired applications. Understand the properties, strengths, and limitations of various materials commonly used in additive manufacturing, such as polymers, metals, or ceramics.
- Start with Small-Scale Projects
Begin with small-scale projects to gain hands-on experience and understand the intricacies of additive manufacturing. This allows you to learn and iterate without significant costs or risks.
- Experiment and Learn from Failures
Don’t be afraid to experiment and learn from failures. Additive manufacturing involves trial and error. Embrace the learning process and iterate on designs and settings to improve outcomes.
- Collaborate and Seek Expertise
Engage with additive manufacturing communities, forums, and experts to expand your knowledge and seek guidance. Collaborate with experienced professionals to gain insights and learn best practices.
- Continuously Adapt and Evolve
Stay updated with the latest advancements in additive manufacturing. Embrace new technologies, materials, and processes as the industry continues to evolve. Continuously adapt and refine your additive manufacturing practices to maximize its potential.
FAQs
Additive manufacturing, also known as 3D printing, is a manufacturing process that builds three-dimensional objects by layering materials on top of each other.
Additive manufacturing offers advantages such as design flexibility, reduced material waste, rapid prototyping, customization, and the ability to create complex geometries.
Additive manufacturing has applications across various industries, including aerospace, automotive, healthcare, consumer products, and architecture, among others.
Yes, additive manufacturing has limitations such as production speed, material selection, post-processing requirements, and certain design considerations for optimal results.
Unlike traditional manufacturing methods, additive manufacturing builds objects layer by layer, allowing for more intricate designs and reducing material waste.
Additive manufacturing can offer cost benefits, particularly for low-volume production, customization, and avoiding the need for tooling. However, cost-effectiveness varies depending on factors like part complexity and material usage.
References
Please take the time to read our post and share it on social media and share your thoughts with us.