additive manufacturing definition
Don’t have time for the complete additive manufacturing definition? Here’s the short rundown: How authoritative is your definition of additive manufacturing? Does it focus on what makes something additive manufacturing, or does it take a thematic approach? Does it describe the techniques used or share some valuable examples? This blog post will define this type of manufacturing, and throughout help, you update your own.
additive manufacturing definition
3D printing, also known as additive manufacturing, is a concept in which it employs various methods to recreate 3D items developed through computer-aided design (CAD). It may perform additive manufacturing on a wide range of materials and does not cause the use of tools or the use of a block of raw material. It is possible to do the task more quickly than standard manufacturing procedures.
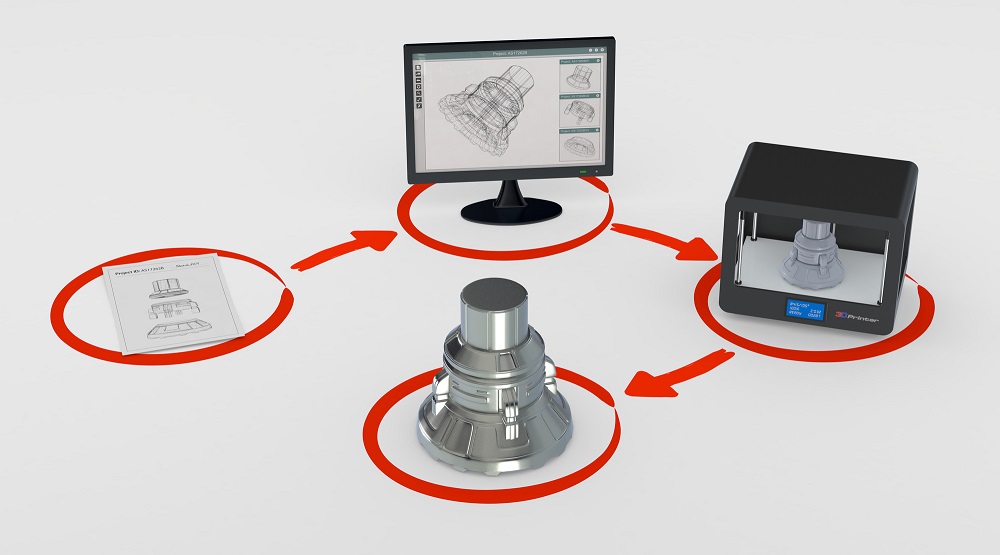
Brief History About Additive Manufacturing
The history of additive manufacturing is the story of humankind’s desire to design, fabricate and construct with ease. The said process has ruled the imagination of many people since ancient times. And as far as recorded history goes, we have always pursued ways to make this concept practical. From founding inkjet to computer-aided machine tools, additive manufacturing is now a global phenomenon that changes how it manufactures products worldwide.
3D Systems commercialized stereolithography in 1987. (SL). The method successfully used a laser to freeze microscopic layers of UV light-sensitive liquid polymer and was the first commercially available AM device. EOS presented their prototype EOSINT M160 machine, which used direct metal laser sintering technology, in 1994. Optomec first launched its Laser-Engineered Net Shaping (LENS) metal powder system in 1998. Röders, a German firm, launched their Controlled Metal Buildup (CMB) machine in 1999. Various polymer-based AM technologies, such as fused deposition (FDM) from Stratasys, Solid Ground Curing (SGC) from Cubital, and Laminated Object Manufacturing (LOM) from Helisys, began commercialization in the early 1990s.
Key Difference between 3D Printing and Additive Manufacturing
Recognizing the critical differences between AM and 3D printing can help us the definition of additive manufacturing.
3D printing is a form of additive manufacturing. However, additive manufacturing is a broader phrase that incorporates more extensive techniques than its 3D printing equivalent. For example, electron-beam manufacturing and selective laser melting are additive manufacturing processes. Neither of these builds layers of material, yet they still involve the creation of objects by adding material. Therefore, electron-beam manufacturing and selective laser melting are additive manufacturing.
It’s also worth highlighting that the word “additive manufacturing” is more typically linked with industrial and commercial uses. In contrast, “3D printing” is most commonly connected with consumer and recreational applications.
The primary distinction between 3D printing and additive manufacturing is that 3D printing includes fabricating items by layering layers of material. In comparison, additive manufacturing involves the construction of objects by adding material, which may or may not arrive in layers.
additive manufacturing process
Slicing an object into thin horizontal layers is the foundation of all additive manufacturing methods. They put each layer on top of the one before making the part.
Stereolithography: A UV laser hardens the areas it sweeps using a liquid photosensitive resin.
Laser powder sintering (SLS/DMLS/SLM) involves using a laser to harden a specific location on a powder bed (metal or plastic).
Powder spraying methods (DMD): A laser hardens a metallic powder thrown onto the preceding layer directly into its beam.
Resin projection methods (Polyjet): Uv light solidifies a photopolymerisable resin applied by a printing nozzle.
Fused deposition modeling (FDM) is a process in which a three-dimensional extruder head deposits thin strands of melted plastic that harden instantly.
Multicolor printing with a bonding agent projection (Zcorp): it dropped fine drops of colored bonding agent upon a powder to agglomerate it selectively
additive manufacturing and subtractive manufacturing
Additive manufacturing refers to creating an object by adding several layers. On the other hand, subtractive manufacturing eliminates or slices away material to make parts. Both processes have separate underpinnings. However, Their use together is justified because some of their applications are similar. The table below compares and contrasts some distinctions between additive and subtractive manufacturing.
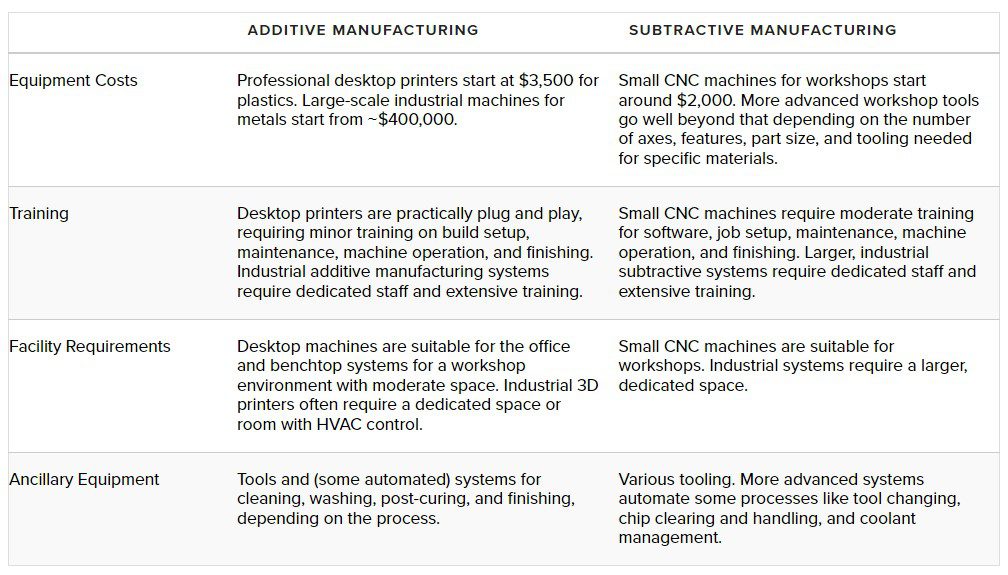
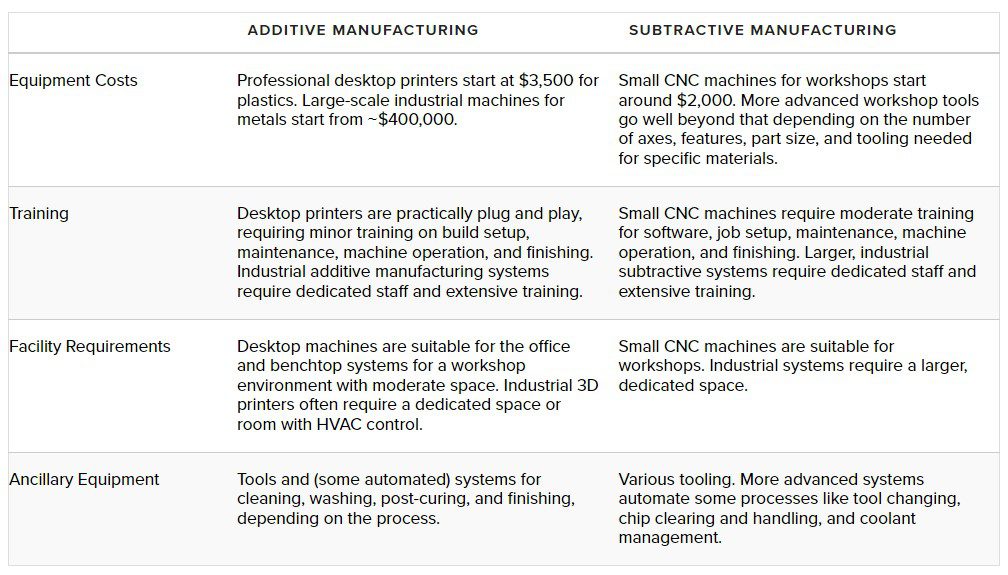
Additive manufacturing advantages
There are various advantages to additive manufacturing. Additive manufacturing enables the rapid and low-cost production of a wide range of prototypes. These particular advantages have some degree of waste reduction and energy savings. AM manufacturing allows for design freedom and innovation without the cost and time constraints of traditional manufacturing. The technique also utilizes less material because it uses what is necessary to create a product.
We know merging production and assembly into a single process as additive manufacturing. Additive manufacturing allows the development of parts that would be impossible to produce using traditional methods such as milling or cutting shapes from steel sheets. AM also decreases the need for tooling, reducing the amount of material required to create components. 8. Reduction of material waste
When combined with the usage of CAD software, this approach allows for quick and straightforward reverse engineering to build legacy parts.
Part flexibility is another important aspect in reducing AM waste. We can divide the benefits of additive manufacturing on supply chains into several categories. With additive manufacturing technology, manufacturers can print entire components with precise tolerances. Producers have fewer unsold products and reduced inventory waste due to this built-in made-to-order technology and the ability to manage small batch orders. AM encourages process flexibility, allowing supply networks to respond to demand more quickly, reduces supply chain risk by providing a contingency plan, and reduces supply-related expenses.
Additive manufacturing disadvantages
Identifying the advantages and disadvantages of the AM can help us with the definition of additive manufacturing.
Some parts require post-processing to remove support material from the build and smooth the surface. Post-processing depends on the size of the part being produced and the intended application. The cost per unit of 3D printing is different from that of other manufacturing techniques. Some printers may have lower tolerances, meaning that final parts may differ from the original design. People are more likely to make fraudulent and counterfeit products while utilizing 3D printers.
Alternative terms for additive manufacturing
Although the technology is around 30 years old, 3D printing has been thoroughly documented and defined in the last few years. People new to the sector frequently ask us if there is a distinction in terminology between 3D printing, additive manufacturing, and rapid prototyping.
There is no distinction between the words 3D printing and additive manufacturing. The terms 3D printing and additive manufacturing refer to the same process. Both words allude to the technique of creating pieces by connecting material from a CAD file layer by layer. In contrast, a typical manufacturing technique, such as CNC Machining, creates a product by eliminating material from a block of material. 3D printing and additive manufacturing can make parts of plastic, metal, or rubber.
As usual, those who work in an industrial or manufacturing environment prefer additive production because it looks more formal. On the other hand, the media favors “3D printing”. However, “3D printing” has become more common due to published documents and the popularity of low-cost desktop printers.
Rapid prototyping is not the same as 3D printing/additive manufacturing. Rapid prototyping is creating a working prototype model from a CAD file. In other words, the process is 3D printing/additive manufacturing, and the end product is rapid prototyping. Rapid prototyping is one of several applications under 3D printing/additive manufacturing.
The 3D printing future
3D printing in the future is currently experiencing a boom. There are probably dozens of new printers being released onto the market as you read this. It feels like a frontier period in the world of printing and prototyping. The notion of ​​printing everyday objects in life is something that we have seen in sci-fi movies and TV shows for a long time. However, as technologies continue to improve rapidly, innovations such as this are not too far away for us.
Main Trends in AM
This tendency may be the clearest, from prototyping to serial manufacturing; after the first phase of AM, which was prototyping, and the second stage, after providing us reduced prices and accessibility through open source, we are in the third stage: the penetration of AM in multiple industries. This stage is not only about prototyping but also about creating finished items. New supporting technologies like simulation and boosting productivity will follow that trend.
FDM Metal: it will increasingly employ metal printing in serial production, as it is cheaper and easier to use than other technologies. In addition, FDM metal gives a superior quality to some of the standard manufacturing technologies.
Hybrid manufacturing:Â This phrase refers to the mix of subtractive and additive processes. When high fineness is required, we utilize additive manufacturing, while we use subtractive manufacturing when standard methods fail. We can achieve a more cohesive environment by combining fabrication and precision.
New Materials: especially in the bioprinting industry (human tissue, etc.)–will open up various options.
High specialization and hardware/software separation:Â We can expect 3D printing companies to specialize in the future rather than being full-stack AM operations.. Hardware companies have to carry their hardware legacy, and for software companies, hardware is too complex to gain a presence in that market. However, if full stack AM firms come up, it will be in emerging areas like bioprinting which do not have the hardware pedigree as industrial AM hardware companies do.
Design revolution: tiny enterprises did this. Interior features are difficult to be generated by a human; hence, there is a movement towards software that concentrates on doing that with an algorithmic method.
Main Problems in AM
Slow technology: Speed is what is eventually needed to make bulk pieces at scale. Today, 3D printing is still too sluggish, but firms like Nexa3D or Desktop Metalwork speed up the process in their sector.
Repeatability: This challenge comes with the shift to serial production. If you print numerous parts, each has to be the same. Machines and software have to be built that ensure that steps are repeated.
Security: A secure mechanism to obtain content into a 3D printer is needed. Today, hackers don’t even need reverse engineering to acquire access to design features. That’s why a big worldwide furniture firm refuses to employ 3D printing since they are concerned that they lose their data once they put it out there.
Quality assurance: This is especially difficult in aerospace or health sectors, where the quality and reliability of printed parts are essential. In these high-value sectors, audibility is vital; businesses like 3dtrust work on this challenge. Right now, 3D printing is not as economical as the traditional production methods. For this reason, giant corporations are reluctant to convert from conventional to additive approaches. Overcoming this challenge requires a boost in productivity, which can be achieved by eliminating all barriers that get in the way.
Not ready / Lack of skills: There were considerable breakthroughs in 3D printing hardware, but the software has fallen behind; therefore, right now, the industry is grappling with a utilization problem. In truth, 3D printing is quite sophisticated, and utilization has to be enhanced by overcoming the Lack of knowledge and the skill barrier. Education is essential, but new solutions such as Generative Design might be a terrific approach to ease the process.
conclusion
That’s it! We hope you learned as much is reading our additive manufacturing definition as we did writing it. If you want to learn more about this topic, check out some of the other posts on our blog. Add something unique to your world.
FAQs
Additive manufacturing, often known as 3D printing, makes products by adding layer upon layer of material until the part is complete. Plastic, metal, concrete, and, one day, even human tissue could be used as the material.
Additive manufacturing (AM) can reshape manufacturing in some industries. When used appropriately, additive manufacturing can significantly reduce material waste, production processes, inventory retained, and the number of separate parts required for an assembly.
merriam-webster:Â Additive manufacturing builds an object up layer by layer instead of the old approach of carving a usable part out of a large block of material.
3D printing (sometimes referred to as Additive Manufacturing (AM)) is the computer-controlled sequential layering of materials to create three-dimensional shapes. A 3D digital model of the item is created, either by computer-aided design (CAD) or a 3D scanner.
Additive manufacturing promotes eco-friendly goods, eliminates waste and junk after the product life cycle, and allows resource-efficient material selections through recycling.